
SECOVAC
International
Where the lumber drying art becomes a science
SECOVAC has developed the most visual, flexible and sophisticated program in lumber drying technology in the last 10 years. The Multizone Control System uses the Temperature Drop Across the Load (TDAL) principle to provide useful information during the entire drying process and to shut the kiln off when the lumber is dry. SECOVAC's fully automated control program in a multi-tasking WINDOWS NT operating environment has been designed to easily adapt to existing control systems using either a PLC or OPTO22 panel to interface with the kiln components. Electronic sensors are used to send data to the computer for automatic evaluation and reaction to the situation.
We leverage our decades of experience in control systems to modify and supplement your existing control system. Our team will visit your operation to provide a diagnostic evaluation of your current control system and recommend upgrades that will result in measured improvements.
SECOVAC's own programmers have developed software to control every aspect of the kiln operation. The following are some of our valuable features:
-
Each segment of the drying schedule has a name corresponding to a program with a pre-defined philosophy of drying. This principle allows a change of segment without altering the current schedule.
-
The Dry and Wet Bulb temperatures can be controlled either at the entering, at the exiting or at the average for each one of the segments, rather than the conventional control on the average or exiting side only, for all segments. This concept allows the use of faster schedules.
-
Useful drying reports for each individual kiln and for the whole system with important information, such as when the charge started and ended, how long it spent in each segment, the number of alarms, running time of the kiln per month, etc.
-
The accuracy of temperature sensors (RTD or T/C) can be verified against a reference temperature and calibrated by software. SECOVAC has designed a Calibrator Oven as a complement to its Dry Kiln Control Software. Together, they establish a calibration curve for each RTD or T/C to eliminate the "sawtooth" effect on the dry bulb temperature graph and reduce the length of the drying schedule for energy savings.
-
We actually control a total of fifty-two (52) kilns with excellent results. Our system has improved the drying time, moisture distributions, and grade of the lumber.
-
Our development efforts in software allow us to customize the program for each customer's specific needs.
-
An internal modem is provided for remote access, as well as yearly software upgrades and service.
-
The SECOVAC's Control System is designed for ease of operation by a dry kiln operator, without a high level of technical computer training.
Following are some of the screens of SECOVAC's Dry Kiln Control program:
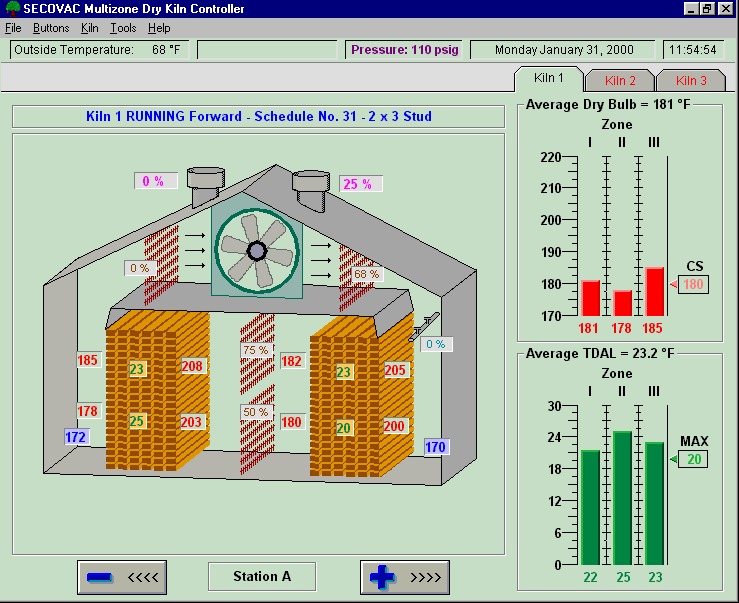
This screen displays the kiln's Cross Section view with vent and valve openings. RTD or T/C values are shown in red for dry bulb temperatures, in blue for wet bulb temperatures and TDALs are green. When you press on a dry or a wet bulb temperature, a contextual menu appears to indicate the OPTO22 or PLC name and address allowing you to put the RTD in or out of service.
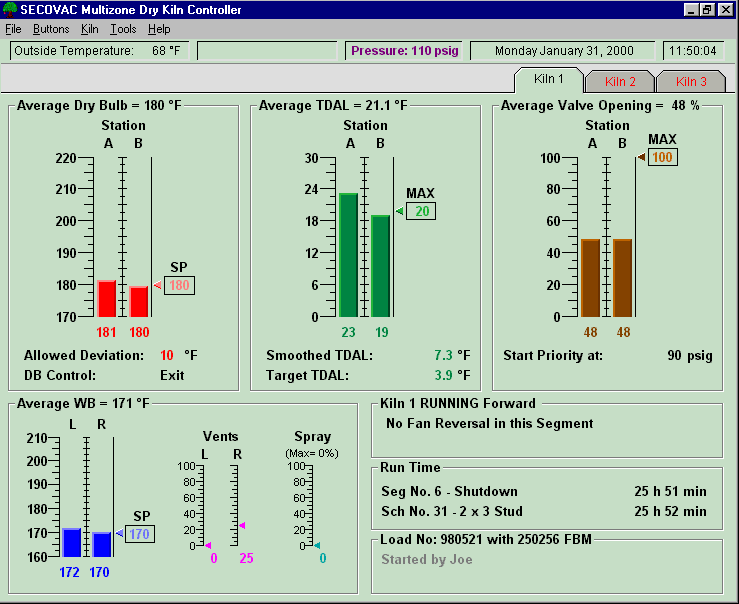
The Status Screen gives you a general view of the entire kiln. SECOVAC's experts have designed this screen to show all the information in "Real WINDOWS" format. The kiln operator can easily verify the bar graphs against the set point (SP) and know, at a glance, the current conditions in the kiln.
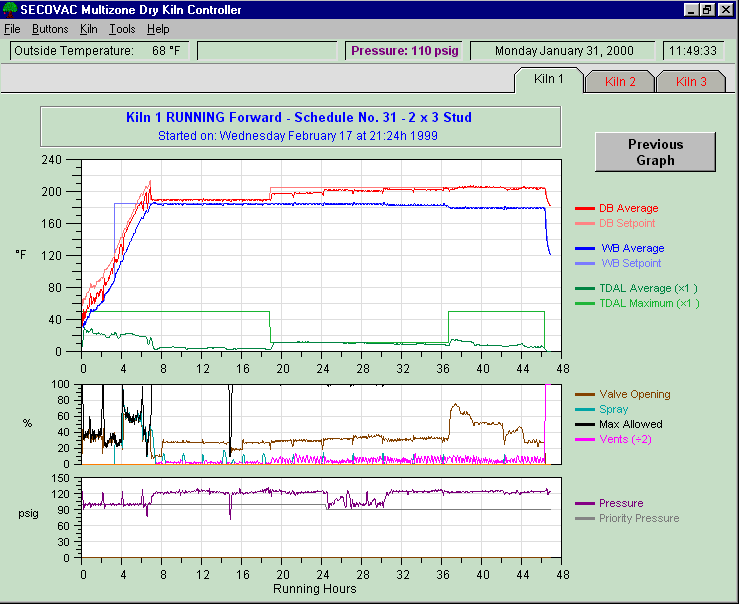
The Graph Screen shows the temperatures, vent and valve openings and pressures display in three parts so it is easier to read and interpret. Retrieving Previous Graphs is accomplished by pressing the specified button on this screen. Having to flip screens is distracting.
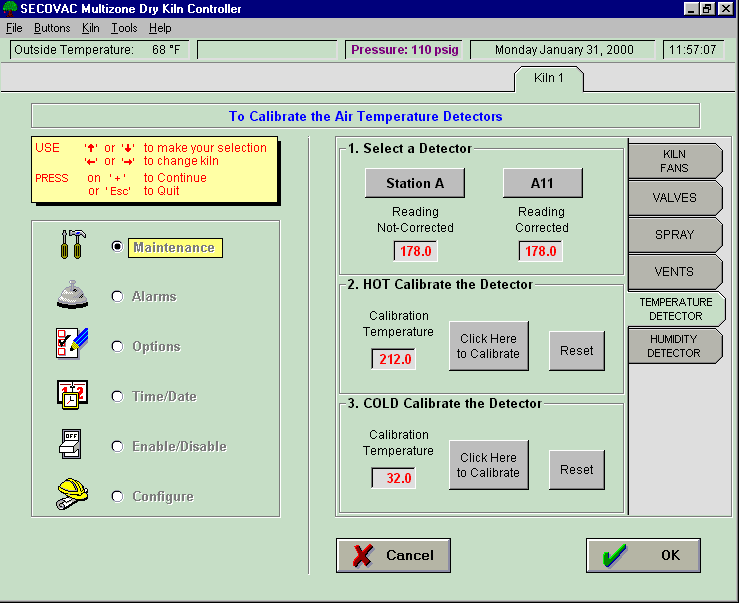
The Calibration of heat sensors is of prime importance ! With SECOVAC's program, it's easy. Follow these three steps as shown in the screen:
-
Select the station and sensor that need calibration
-
Insert the sensor in the Calibration Oven for 5 minutes and press "Click here to Calibrate"
-
Re-insert the sensor in a mix of ice and water for another 5 minutes and press "Click here to Calibrate".
Our program takes care of the rest. A calibration curve is established between the two points and used to calculate the calibrated temperature each time a sensor is read.